This maintenance tutorial addresses TT250 valve adjustment.
You’ll need the following tools for this operation:
- A pair of pliers
- 14mm socket with ratchet and extension
- Spark plug wrench
- 10mm wrench
- Long handled Phillips head screwdriver
- Large bladed flat head screwdriver
- 6mm Allen wrench
The TT250 has a two-valve engine. The intake valve opens to admit the fuel/air mixture, and the exhaust valve opens to expel the exhaust. When the engine is at the top of its compression stroke, we want both valves closed. That’s because we want to compress the fuel air mixture, ignite it, and then allow the resulting high combustion pressures to drive the piston down. If any leakage occurs around any of the valves while this is occurring, the engine will lose power and it could “burn” a valve if the combusting fuel/air mix escapes around the valve while it is still burning.
When engineers design an engine, they want it to do the above, but they have to account for the thermal expansion that occurs as engine temperature increases during normal operation. In order to compensate for this thermal expansion, the engineers design in a gap in the rocker arm/valve train. As the engine warms, this gap approaches zero, and everything works the way it is supposed to.
On the TT250, the valve train looks like you see in the photo below (this photo shows the exhaust valve, but both the intake and the exhaust valve have similar valve trains). The valve gap (also referred to as the valve clearance) is what the lower red arrow points to in the photo below.
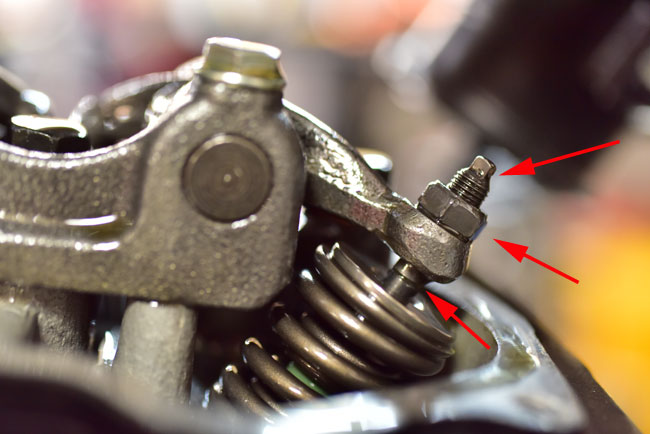
As the wear described above increases, it has the effect of reducing the valve gap (i.e., the clearance built into the valve train to account for the thermal expansion as the engine warms up). What happens is that as this wear occurs, the valve actually moves higher into the cylinder head and the valve gap decreases. If this wear goes beyond acceptable limits without adjusting the valves, the valve gap grows smaller and smaller. Ultimately, this wear will result in the valve being held off the seat when combustion occurs. This is bad, because when this condition exists, hot burning gases escape around the valve sealing area. Ultimately, these burning gases will destroy the valve and the seat. That’s what happens when we “burn a valve.” It’s also bad because the valve needs to cool, and it is cooled primarily when it is closed against the valve seat. That allows heat to escape from the valve and flow into the cylinder head. If the valve never fully closes, the valve will continue to heat, and the valve stem will expand diametrically so much that it seizes in the valve guide. That’s really bad, too, because when that happens, the valve will stick, the piston will hit it, and you’ve just bought yourself a new engine (or you’ll have to pay for expensive repairs on the current engine).
If the above sounds really bad, relax. We avoid it by adjusting the valves. All we are really doing is keeping the gap in the valve train within an acceptable range over the life of an engine. As the valve and the valve seat wear, we keep everything adjusted so that when the engine is at operating temperature we still form a good seal around the valve seat. That’s the whole idea behind this valve adjustment business.
Different engines use different approaches for adjusting the valves. Your TT250 engine uses the best approach for easy maintenance and high performance: It uses a threaded adjustor shaft with a lock nut to set and lock the valve gap. In the photo above, that’s what the upper two arrows point to. These adjustors are located in the ends of the rocker arms that interface directly with the valve stem.
So, with all that theory behind us, let’s consider what we’re going to do here:
- We want to gain access to the valve rocker arms and their adjustment screws.
- We want the engine to be at a point in its rotation such that the rocker arm is on the cam’s base circle. This means the cam is not actuating the rocker arm. We want the engine to have the piston at (or very near) top dead center, which means the valves should be closed (which is another way of saying the rocker arm is on the cam’s base circle).
- With the engine in this position, we want to loosen the threaded adjustor lock nuts, we want to set the valve gaps to the specified gap of 0.04mm to 0.07mm, and we want to tighten the lock nuts to lock the threaded adjustors at this gap. We always make the adjustment to the 0.07mm setting. As the valve and the cylinder head wear, the gap will grow smaller. Setting it to the 0.07mm setting allows us to keep the valve adjustment interval (the number of miles you can ride between valve adjustments) at a reasonably high number. Initially, we’re establishing this interval to be 500 miles for the first adjustment, and every 2500 miles thereafter.
- When we’ve completed the above, we want to put everything back together.
Got that? Okay, here we go….
Most of the work in adjusting the valves is associated with just getting access to the adjustors. The adjustment operation (once we have access) takes only a few minutes.
When you adjust the valves, you have to start with a cold engine. Dead cold. Let your TT250 cool down completely. Don’t cheat on this part. I always let the bike set, without starting the engine, for a day. If it’s even a bit warm from running, your adjustment will be wrong, and all of your work will be for nothing. Let your TT250 cool down completely.
Remove the rear body panels on the left and right side of the motorcycle.
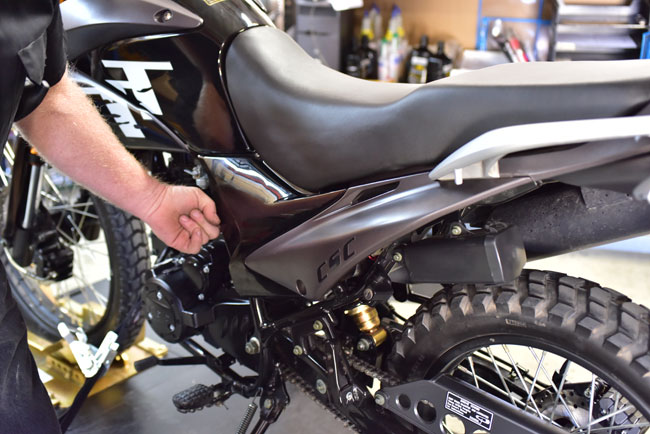
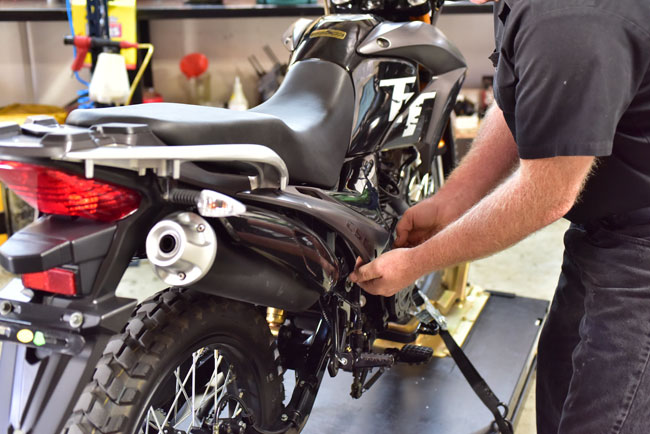
Remove the seat. It’s secured by 10mm bolts on either side. Once the bolts have been removed, the seat slides to the rear.
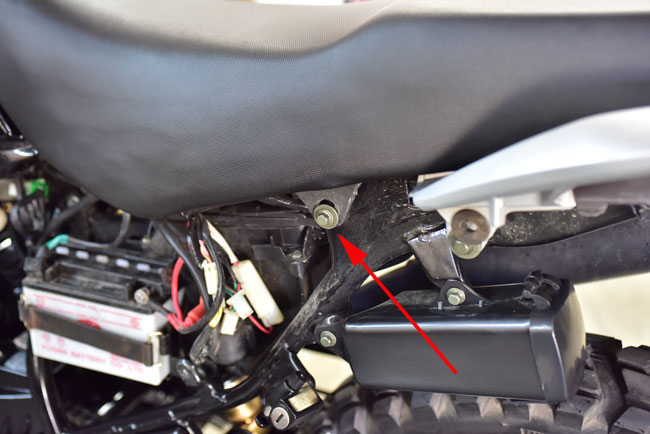
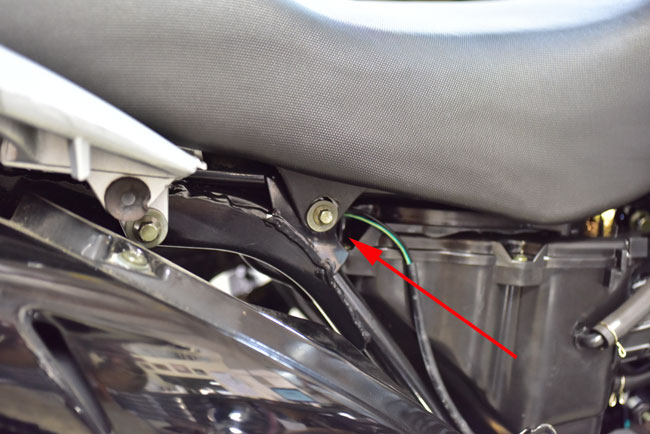
Close the fuel petcock and remove the fuel hose from it.
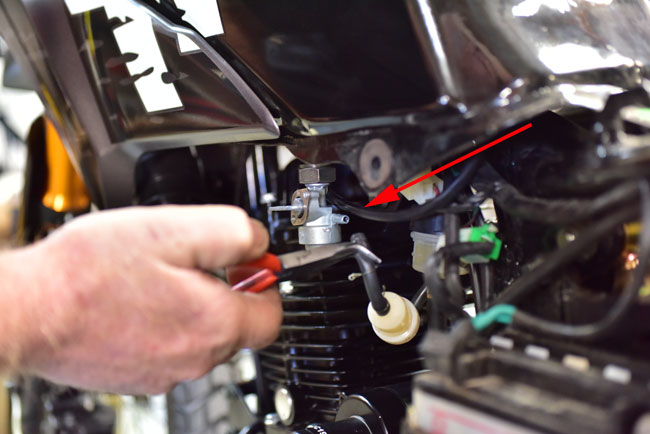
Remove the hose from the right upper hose boss on the carbon canister. The other end of this hose remains attached to the fuel tank.
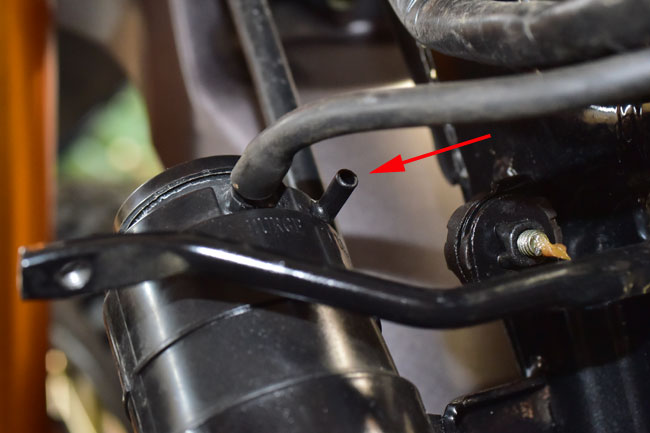
Remove the 10mm bolt at the base of the fuel tank. You’ll see it after you have removed the seat.
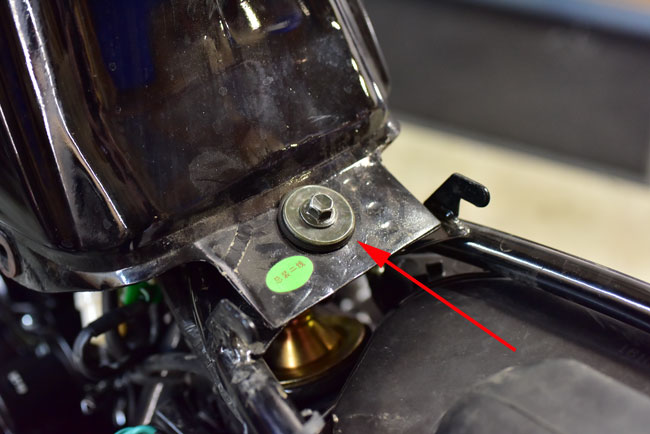
Remove the two screws that secure the left and right fuel tank body panels to the frame. You do not need to remove the body panels from the fuel tank.
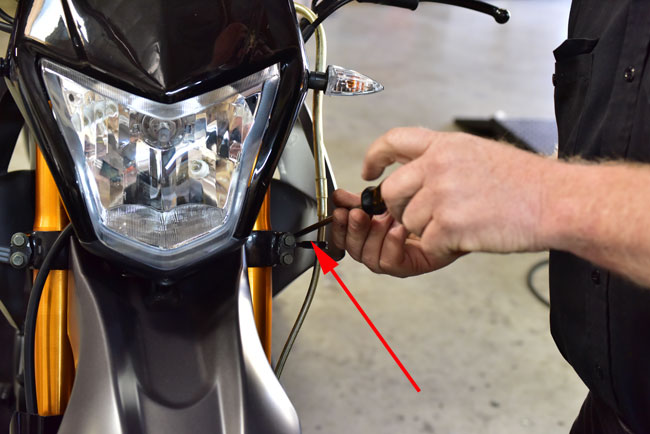
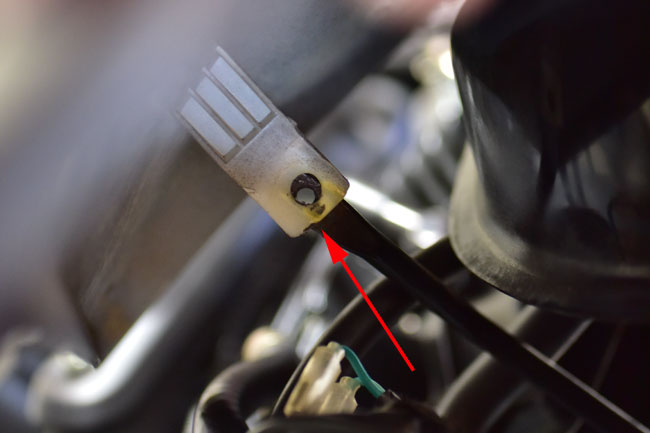
Slide the fuel tank to the rear. After you have lifted it partially off the motorcycle, disconnect the electrical connector that runs from the fuel tank sending unit to the fuel gage.
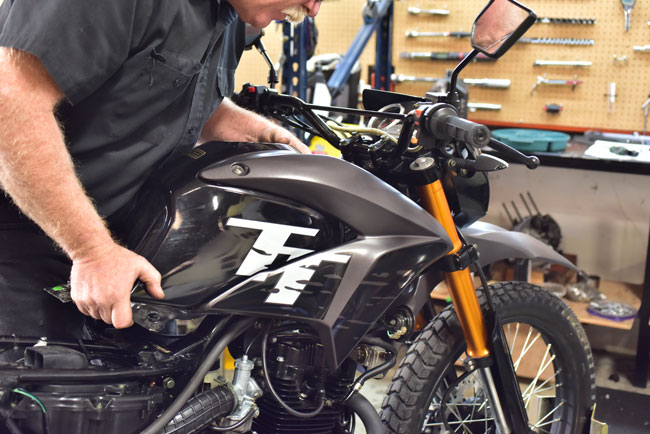
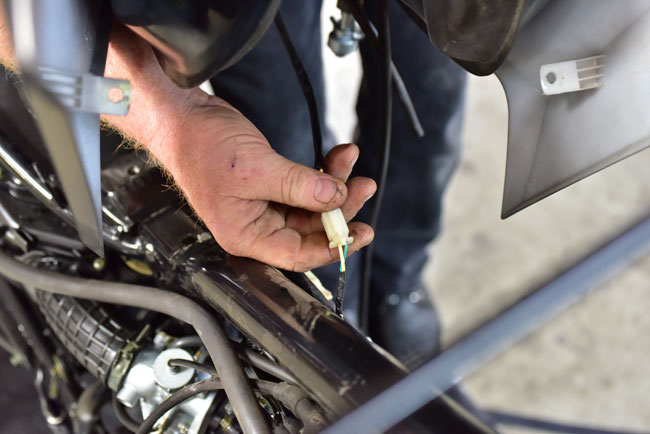
When you remove the fuel tank from the motorcycle, two hoses will hang down. The longer one is the fuel tank overflow line. It simply hangs down from the fuel tank; the other end is not attached to anything (it vents to atmosphere). The shorter hose is the one that attaches to the carbon canister. You’ll have to reinstall the end of it on the carbon canister boss when you reinstall the fuel tank after adjusting the valves.
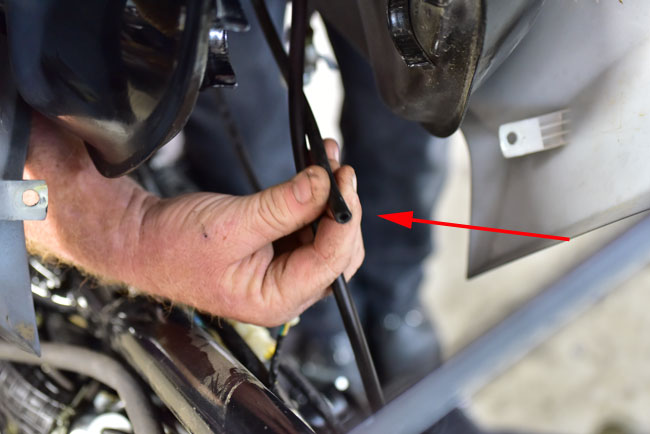
At this point, we have what we want, and that’s access to the valve cover.
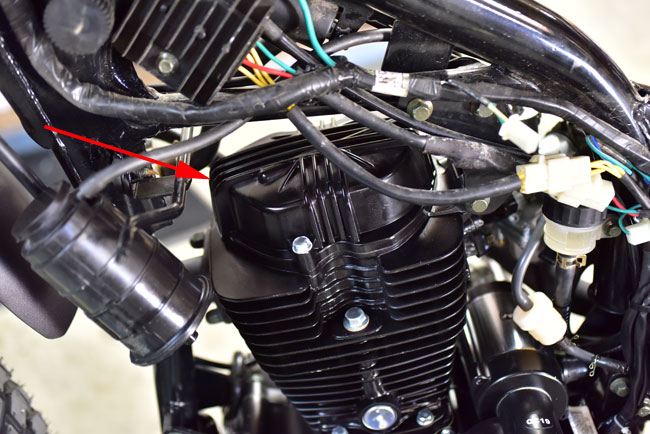
The valve cover is attached to the cylinder head by three 10mm bolts. Note that there is a fourth 10mm bolt on top of the valve cover (it’s the one in the photo below just beneath and partially behind the hose). Leave that bolt alone (do not remove it from the valve cover). Do remove the three bolts that attach the valve cover to the cylinder head.
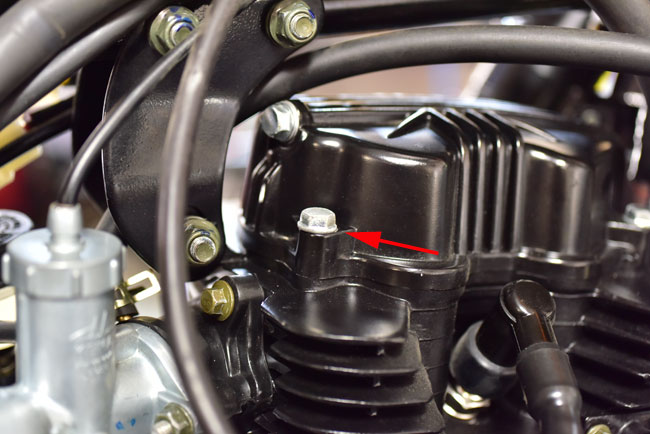
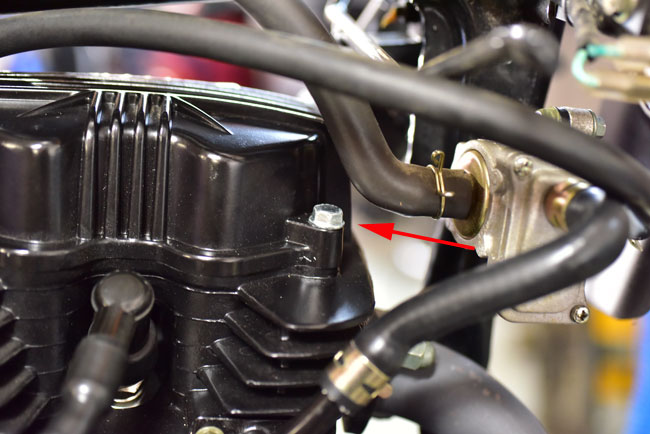
Detach the large diameter hose from the exhaust gas recirculation valve shown below.

Tap the valve cover gently to break the seal between it and the cylinder head.
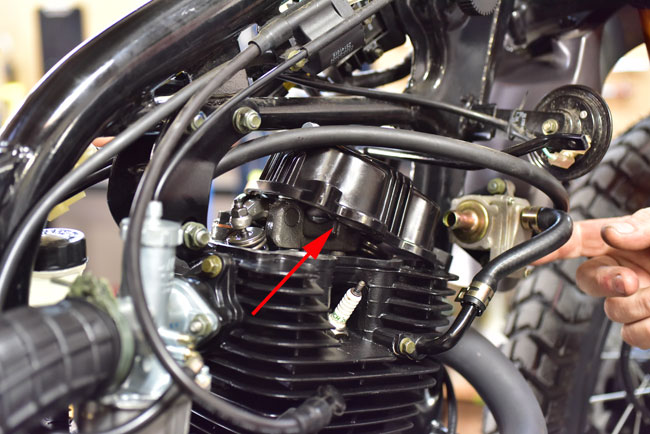
Remove the valve cover. It will remove to the right side of the motorcycle.
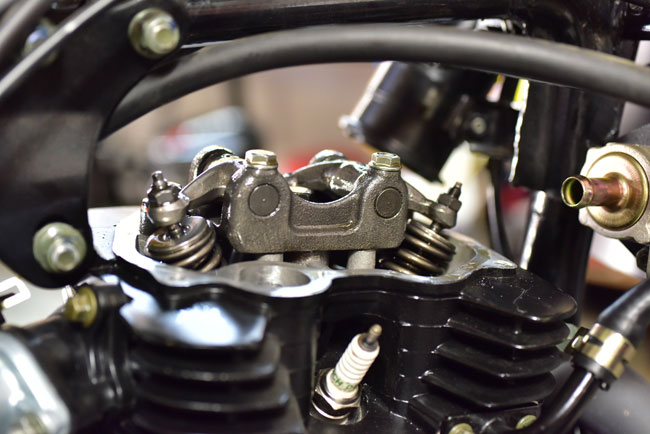
The valve cover seals to the cylinder head with an o-ring type seal. Place the valve cover where this seal will not be contaminated by dirt or debris. Prior to reinstalling the valve cover (after you have adjusted the valves), apply a light coat of motor oil to the rubber seal.
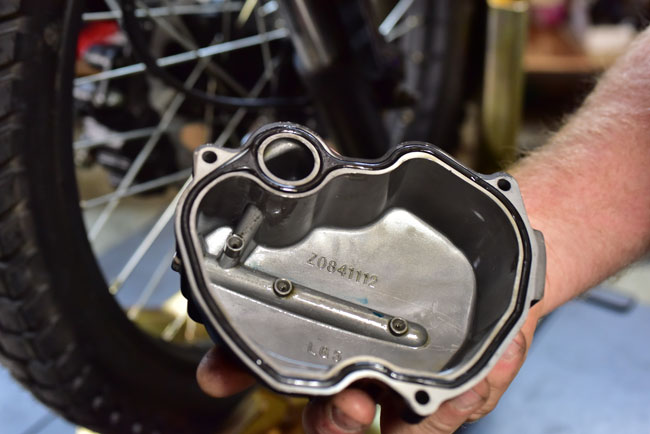
Remove the spark plug.
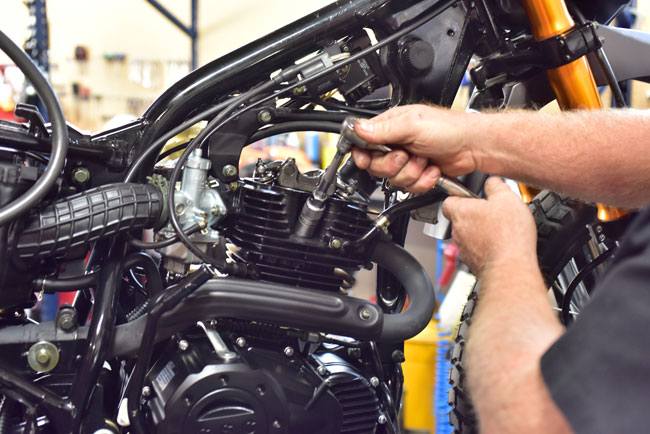
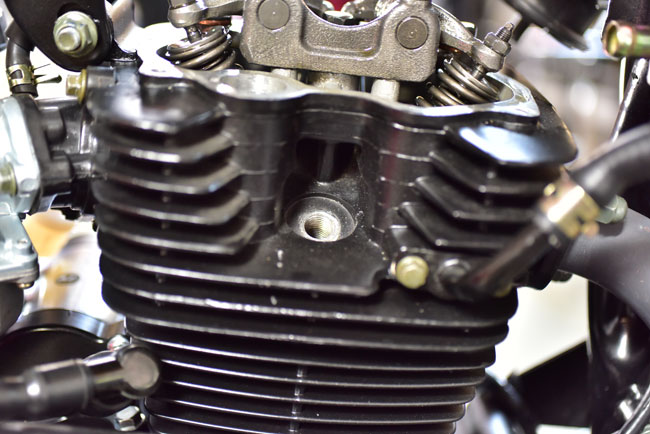
Remove the left crankcase engine cover. It is secured with three Phillips head screws.
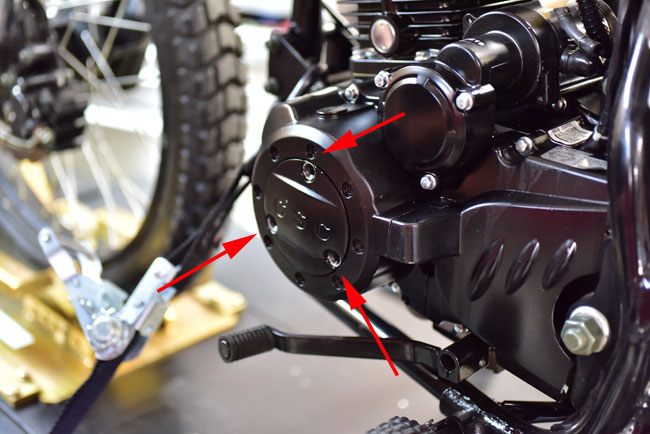
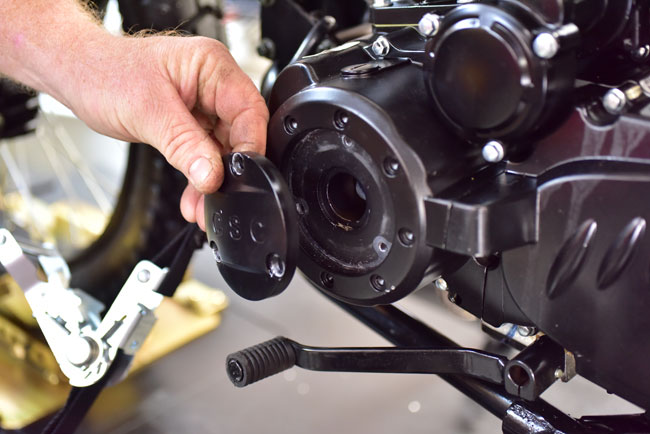
After you have removed the cover, you will see a 14mm bolt head. By placing a socket wrench on this bolt head, you will be able to rotate the engine (it’s why we removed the spark plug). If you have the bike in the vertical position (straight up and down), only a tiny amount of oil will escape. If the bike is on the sidestand, more oil will escape.
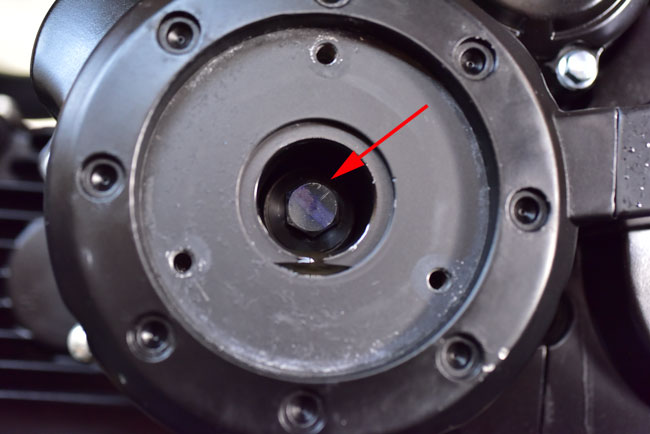
Remove the timing port cover on the left side of the engine with a large blade screwdriver or a coin.
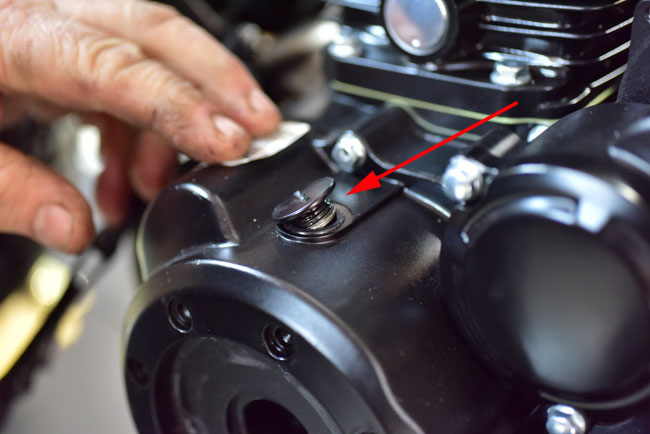
When you remove the timing port cover, take care not to lose the o-ring that seals it. Place the o-ring in an area where it will not become contaminated with dirt or debris.
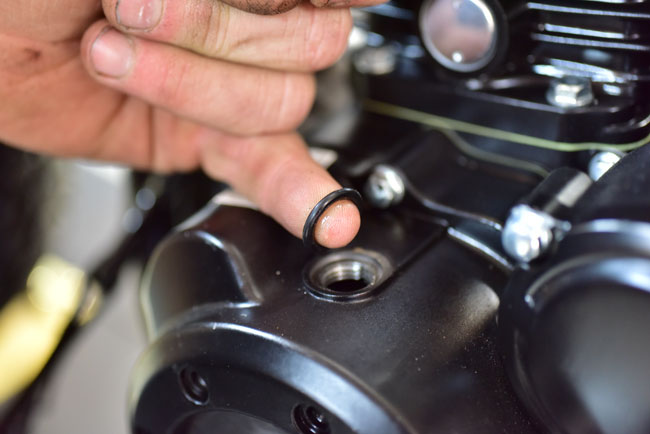
Rotate the engine by hand by attaching a 14mm drive to the crank bolt.
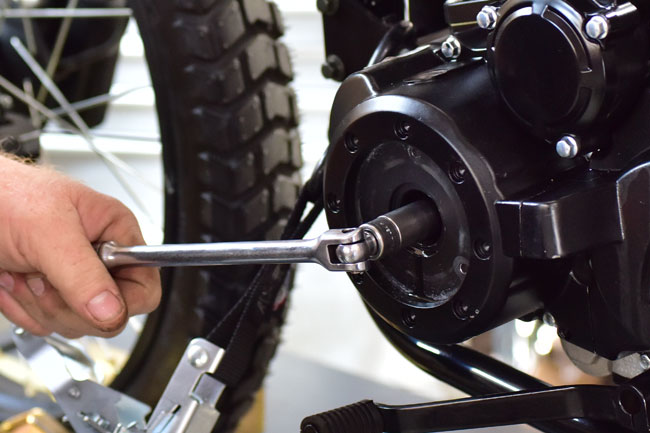
There are three timing marks on the crank shaft indicator wheel. One is a double scribe line that shows when the ignition is fully advanced. We’re not interested in that one for the valve adjustment operation; this information is included here for reference only.
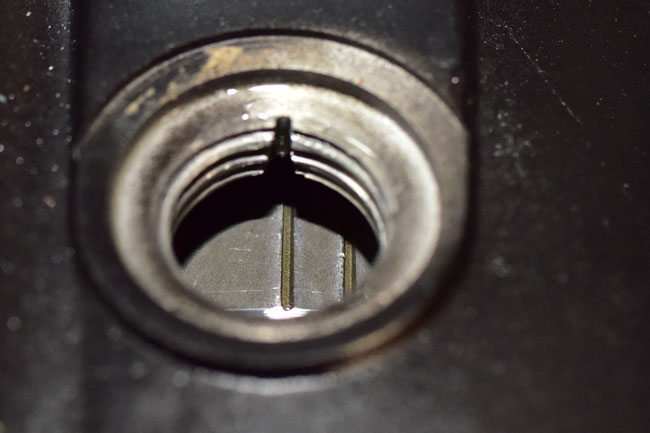
The next mark is a scribe line with an F. This shows when the spark plug fires. We’re not interested in that mark, either, for the valve adjustment operation. It’s mentioned here for reference only.

Here’s the mark we’re interested in. It’s a scribe line with a T. That shows when the piston is at top dead center, which is where we want it to be for the valve adjustment operation.
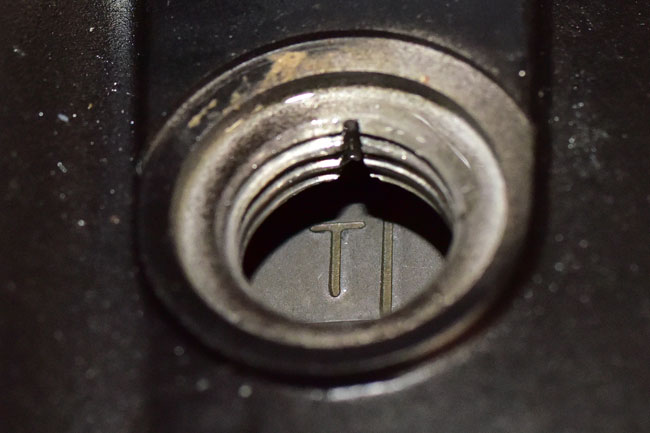
This business of aligning the T mark and its scribe with the slot in the threaded area is a little tricky. You should manually rotate the engine so that this T mark and the scribe line are aligned with the slot and both valves are fully closed. Rotate the engine’s crankshaft through the full 360 degrees at least twice to understand what it going on here. On one rotation, you may see that one of the valves is not fully closed. If that’s the case, DO NOT adjust the valves with the engine crankshaft in this position. Rotate the engine another 360 degrees to bring the T mark and scribe line into alignment with the slot in the threaded area. Both valves should be fully closed, which is to say that the rockers should be in the full up position and the valve gap is fully open for the both valves.
Once the engine is at top dead center as described above, we’re ready to make the adjustment. We’ll do so by loosening the 10mm nut (shown by the middle arrow in the photo below) enough to allow us to rotate the threaded adjustor (shown by the upper arrow in the photo below). By doing this, we are changing the valve gap (shown by the lower arrow in the photo below).
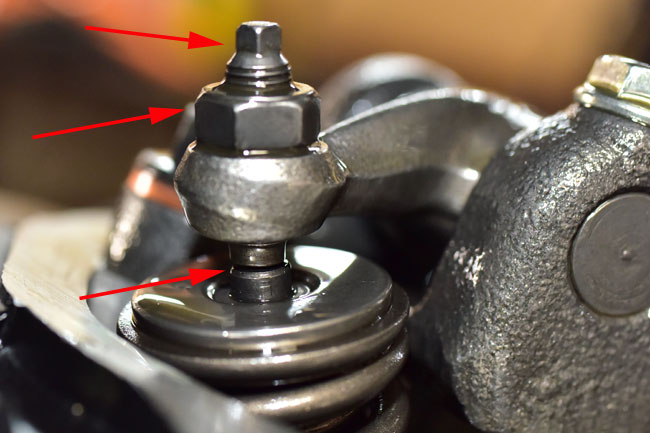
Loosen the threaded adjustor enough to allow insertion of a 0.07mm feeler gage into the valve gap, as shown below.
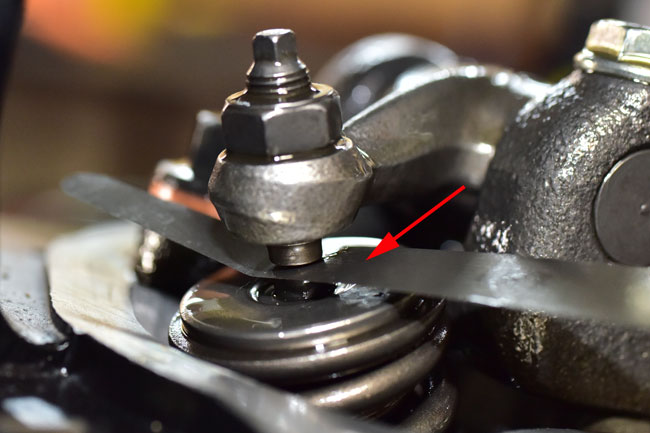
Hand tighten the adjustor so that it is snug against the feeler. You don’t want to overtighten the adjustor or you will start to open the valve and your adjustment will be incorrect. Just make it snug so that if you try to pull the feeler out, you feel slight resistance. Tighten the 10mm adjustor lock nut.
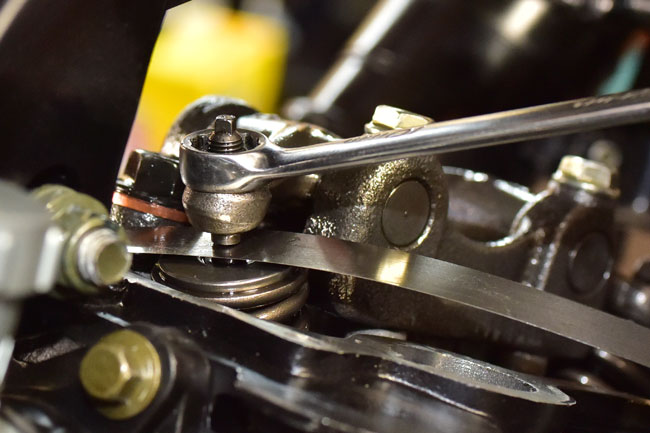
Repeat the above process for the other valve.
After I’ve done this, I manually rotate the engine two complete revolutions, align the T mark and the scribe line again, and check the clearance just to make sure I did it correctly.
Assembly is the reverse of disassembly.
Once you’ve reassembled the motorcycle, go out and put some miles on it!